Scientists just put a 3D printer in space. This is a huge deal for space travel.
Mars, here we come
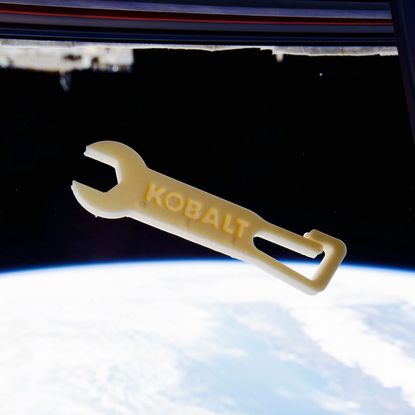

On April 13, 1970, an oxygen tank on a spacecraft carrying three Apollo 13 astronauts to the moon exploded.
"Houston, we've had a problem here," command module pilot Jack Swigert famously said upon feeling his ship rattle and seeing the glow of the warning lights. In that instant, the crew's hopes of reaching the moon vanished. They were 200,000 miles from home, stuck in a crippled spacecraft, and to make matters worse, they were running out of air. They needed a new air filter.
Back on Earth, a team of engineers sprang into action. Using only materials the team had on board their spacecraft, they fashioned a makeshift carbon dioxide filter out of plastic bags, cardboard, and duct tape. Mission control radioed the instructions to the astronauts, who created a replica within about an hour. Mercifully, the filter worked, and CO2 levels in the ship stabilized. This MacGyvered contraption allowed the team to survive the return trip back to Earth.
Subscribe to The Week
Escape your echo chamber. Get the facts behind the news, plus analysis from multiple perspectives.
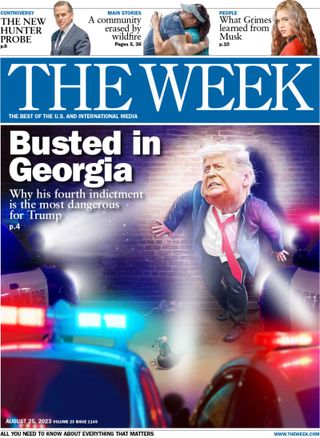
Sign up for The Week's Free Newsletters
From our morning news briefing to a weekly Good News Newsletter, get the best of The Week delivered directly to your inbox.
From our morning news briefing to a weekly Good News Newsletter, get the best of The Week delivered directly to your inbox.
Space travel is unpredictable. So much can go wrong, and it's impossible to plan for and respond quickly to all of it. As a result, we're limited in how far we can go, and for how long. But that's changing. Right now, orbiting 250 miles above Earth on the International Space Station, sits a tool that could revolutionize human space travel: a 3D printer.
"Space is the final frontier," says Andrew Rush, CEO of Made in Space, the company behind the printer. Rush says his team members are "just a bunch of guys who want to see people live and work in space in a sustainable, ongoing way." To help make that happen, they teamed up with hardware store Lowe's to design the device, which arrived at the ISS earlier this year.
If an astronaut needs something — say they let go of a tool and it floated off, never to be seen again — a design team back on Earth creates blueprints that can be uploaded to the 3D printer's system. The object can then be manufactured onboard the ISS and be in the astronaut's hands within a day.
Designing a 3D printer for space wasn't easy. It took a lot of iteration (and trips on the vomit comet) to get right. "You have to build something that's both very rugged and reliable and remotely operated, and something that can operate without the benefit of gravity," says Rush. "We also had to make it really safe for the astronauts." 3D printers spew a lot of noxious gas, which is a no-go in a floating tin can. So Made in Space and Lowe's designed their printer to capture these particles and filter them out. So, as a bonus, the machine actually cleans the air on the ISS while it operates. "That lets the ISS crew live and work with this manufacturing device in their home in space with confidence they're gonna be healthy," Rush says.
Sign up for Today's Best Articles in your inbox
A free daily email with the biggest news stories of the day – and the best features from TheWeek.com
In June, the 3D printer produced its first tool: a Kobalt-branded wrench optimized for space. The printer already has a 6-month queue of projects waiting to be manufactured by researchers here on Earth.
Putting a 3D printer in orbit has huge implications for short- and long-term space travel. Until now, anything astronauts wanted either had to be sent up with them at launch, or delivered later during a resupply mission. Both options are expensive and can take days or weeks. In a dire situation, that's not good enough.
Now, instead of having to wait for a resupply or hack a tool from scraps, the crew can press a button and make one in a matter of hours. "It's building responsiveness into the system," says Spencer Pitman, head of product strategy at Made in Space. "The worst thing that could happen is one of the things you didn't bring with you becomes the necessary thing."
Think of space disaster films like Apollo 13 and The Martian, says Rush. "What if Jim Lovell and Mark Watney had 3D printers? How would that have changed the story?"
Suddenly, it's no longer "Houston, we've had a problem." It's "Houston, we've had a problem, but we're printing a fix right now."
Aside from being a safety buffer, 3D printing (or additive manufacturing, as it's called) also lowers the barrier to entry for experimentation in an environment that, until recently, was only available to a handful of people. It opens the door to playfulness, curiosity, and experimentation without the high stakes (and high cost) of a space launch. "It allows people to feel they can try different things without having to commit as much," says Kyle Nel, executive director of Lowe's Innovation Labs. Along with tools, the printer is creating medical devices and materials for the International Space Station's many ongoing science experiments.
But perhaps the biggest impact of 3D printing in space is that it brings us one step closer to becoming truly independent space travelers. It releases us from our Earthly bounds, untethers us from our home planet. We could produce, literally out of thin air, nearly anything, most notably, settlements on other planets.
"If we go to Mars," Rush ponders, "are we going to repeat Apollo, go and hang out for a bit and come home and never visit for another 50 years? Or are we going to go and stay? If we go and stay, we have to have some manufacturing ability. The difference between a camping trip and settling somewhere is the tools you take with you, and we aim to make the tools that let you, if you want, to go to those places, and then stay and live."
Create an account with the same email registered to your subscription to unlock access.
Jessica Hullinger is a writer and former deputy editor of The Week Digital. Originally from the American Midwest, she completed a degree in journalism at Indiana University Bloomington before relocating to New York City, where she pursued a career in media. After joining The Week as an intern in 2010, she served as the title’s audience development manager, senior editor and deputy editor, as well as a regular guest on “The Week Unwrapped” podcast. Her writing has featured in other publications including Popular Science, Fast Company, Fortune, and Self magazine, and she loves covering science and climate-related issues.
-
Magazine interactive crossword - May 3, 2024
Puzzles and Quizzes Issue - May 3, 2024
By The Week US Published
-
Magazine solutions - May 3, 2024
Puzzles and Quizzes Issue - May 3, 2024
By The Week US Published
-
Magazine printables - May 3, 2024
Puzzles and Quizzes Issue - May 3, 2024
By The Week US Published